I got side tracked from working on my chassis but it was in a good way and thought some of you might enjoy seeing the progress on my new oil pan.
What I’m basically doing here is copying the Canton Road Race pan in aluminum with a few improvements. The major benefit is the cooling effect the aluminum with have on the oil as well as the engine itself. I’m a big fan of passive cooling, 1/3 of the engine heat is radiated to ambient off the external surfaces so in effect the engine is air cooled almost as much as it is water cooled. Not many people think of engine cooling from this prospective but that's a pretty huge number. This pan will have the same effect as a small oil cooler where I might even be tempted to scrap factory oil-to-water cooler rather than dumping that heat into the coolant for the rad to deal with. The baffling here is designed to maximize the amount of oil around the pick-up under “G” in all directions
This is probably not worth the effort for most but I enjoy doing this kind of thing and its fun figuring out where you can make improvements.
This pile of metal is everything needed to get started with some assembly required. It’s mainly 3/16” thick 6061 with ½” thk flanges and the bottom is ¼” to protect it in the event of bottoming out the pan. The baffles are 1/8”. 5052 was used where I needed to make bends. The metal was sourced from Industrial Metal Supply ……… of course! I made cardboard cutout patterns and transferred them to the aluminum plate. The metal was cut with a jig saw using a coarse blade.
Here I laid out the cut pieces to give you a better scope on where everything fits together.
Here is the sump fit check. Note the baffled oil trap. This is one area of improvement I made over the Canton pan which has a strip of metal running along the bottom of the trap door which will impede oil flow into the chamber. I maxed the size of the box allowing for a higher volume of oil surrounding the pick-up and there is no obstruction on the floor of the pan. Any oil that wants to slosh to the other side of pan during high G’s will have to pass thru this box where it will get trapped. I added gussets to reinforce the bottom of the sump and to minimize oil sloshing around in each chamber.
This is a lot of work that pile of metal took me 2 weekends and perhaps a few nights in between to get to that stage. Cutting, fitting and then prepping everything for welding. The thick flanges are to allow for facing off the top flat in the event of warping from all the welding though I don’t think I’m going to be a problem with ½” plate (I’ll skim it down to 3/8” thk when finished).
I’m off to the TIG welder on Saturday. This won’t be finished for a few weeks there is a lot of welding involved here, more fitting, machining and pressure testing. There is also a cover that caps off the sump that prevents oil from splashing away from the sump that needs to be made. This is going to be one bad ass mo fo mod motor wet sump, I’ll post pics as I make progress.
:rockon:
What I’m basically doing here is copying the Canton Road Race pan in aluminum with a few improvements. The major benefit is the cooling effect the aluminum with have on the oil as well as the engine itself. I’m a big fan of passive cooling, 1/3 of the engine heat is radiated to ambient off the external surfaces so in effect the engine is air cooled almost as much as it is water cooled. Not many people think of engine cooling from this prospective but that's a pretty huge number. This pan will have the same effect as a small oil cooler where I might even be tempted to scrap factory oil-to-water cooler rather than dumping that heat into the coolant for the rad to deal with. The baffling here is designed to maximize the amount of oil around the pick-up under “G” in all directions
This is probably not worth the effort for most but I enjoy doing this kind of thing and its fun figuring out where you can make improvements.
This pile of metal is everything needed to get started with some assembly required. It’s mainly 3/16” thick 6061 with ½” thk flanges and the bottom is ¼” to protect it in the event of bottoming out the pan. The baffles are 1/8”. 5052 was used where I needed to make bends. The metal was sourced from Industrial Metal Supply ……… of course! I made cardboard cutout patterns and transferred them to the aluminum plate. The metal was cut with a jig saw using a coarse blade.
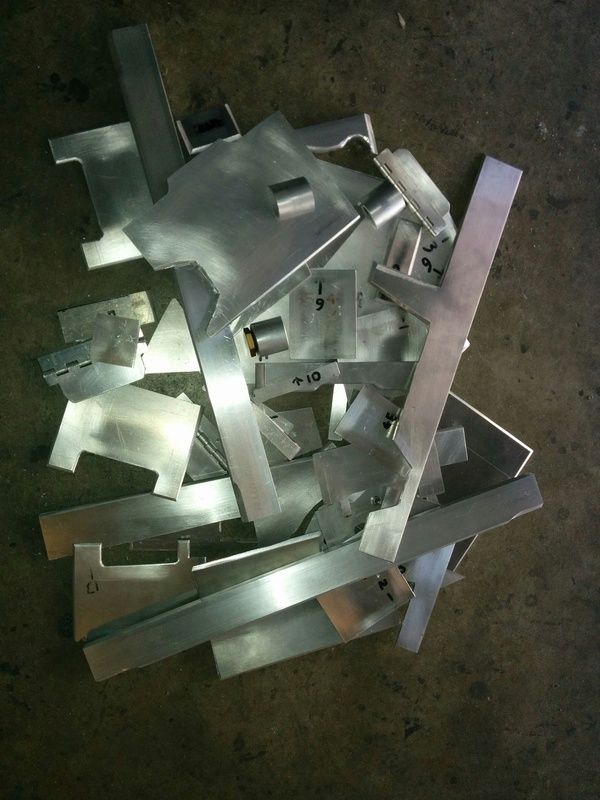
Here I laid out the cut pieces to give you a better scope on where everything fits together.
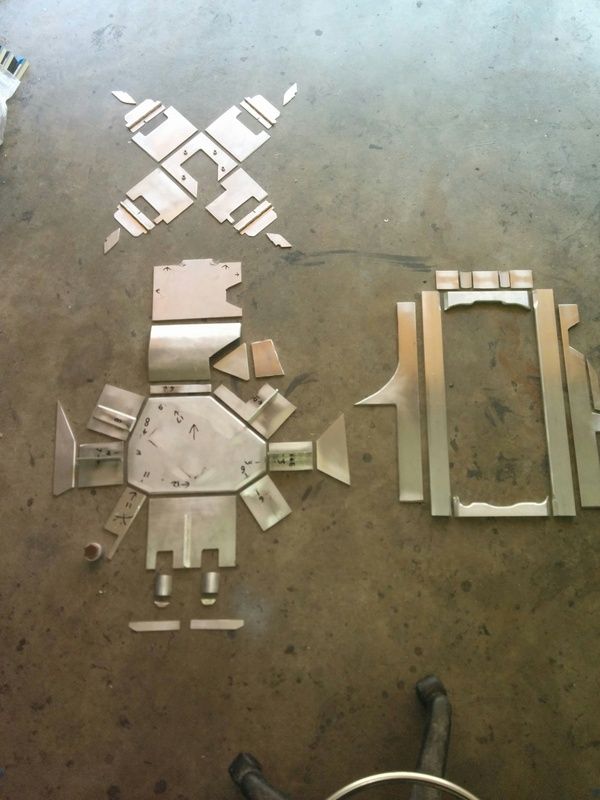
Here is the sump fit check. Note the baffled oil trap. This is one area of improvement I made over the Canton pan which has a strip of metal running along the bottom of the trap door which will impede oil flow into the chamber. I maxed the size of the box allowing for a higher volume of oil surrounding the pick-up and there is no obstruction on the floor of the pan. Any oil that wants to slosh to the other side of pan during high G’s will have to pass thru this box where it will get trapped. I added gussets to reinforce the bottom of the sump and to minimize oil sloshing around in each chamber.
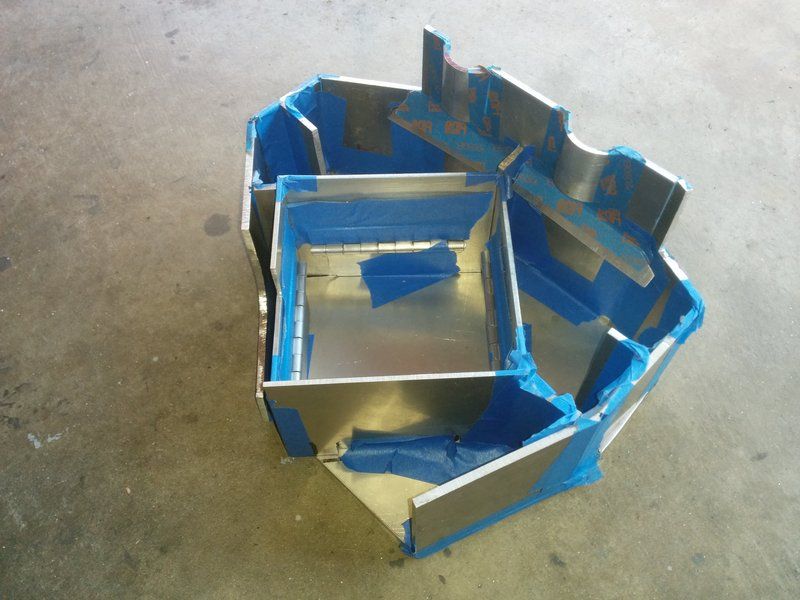
This is a lot of work that pile of metal took me 2 weekends and perhaps a few nights in between to get to that stage. Cutting, fitting and then prepping everything for welding. The thick flanges are to allow for facing off the top flat in the event of warping from all the welding though I don’t think I’m going to be a problem with ½” plate (I’ll skim it down to 3/8” thk when finished).
I’m off to the TIG welder on Saturday. This won’t be finished for a few weeks there is a lot of welding involved here, more fitting, machining and pressure testing. There is also a cover that caps off the sump that prevents oil from splashing away from the sump that needs to be made. This is going to be one bad ass mo fo mod motor wet sump, I’ll post pics as I make progress.
:rockon: